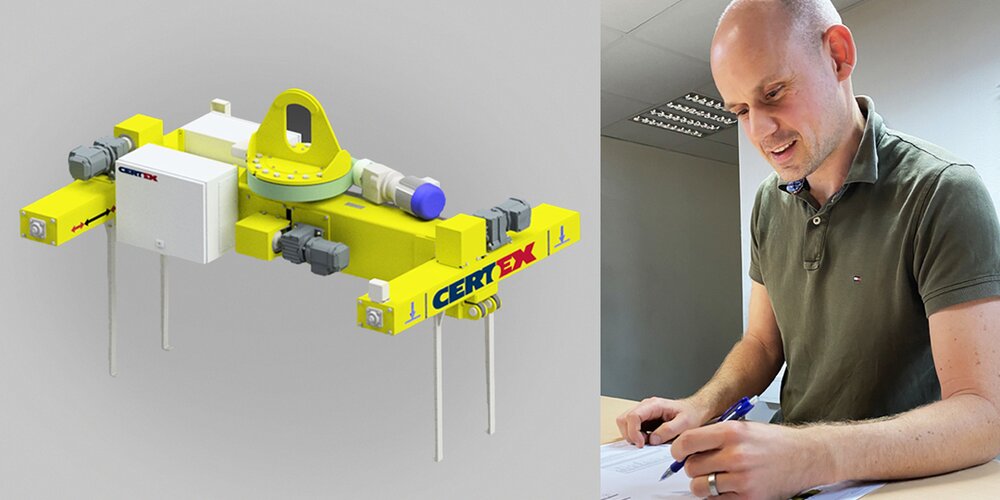
Risky high-altitude mission
CERTEX has many sister companies around Europe. When a customer in Greece saw a lifting need that required a unique, never-before-designed solution, the assignment fell on Special Products in Varberg. Daniel Bokne, designer, talks about the challenge of lifting reinforcing mats in bundles of over four tons.
What was the customer's needs?
- The customer in Greece manufactured reinforcing mats. In the factory, the staff climbed onto the four, five-meter-high bundles and connected chains manually. There was a high risk of injury and many risk factors. Therefore, a need arose for an automated system that solved the management risk-free.
What were the challenges in the project?
- The customer had a loading process where the reinforcing mats were to be lifted from the warehouse onto trucks, but where no part of the lifting tool was allowed to stick outside the surface of the mats when loading. This is because they wanted to use the space in the truck as much as possible.
The mats came in a variety of sizes and had different sized holes; therefore, it was a challenge to come down and grip the load. If you went down too far towards the middle, they weighed down at the edges and vice versa. The challenge was to grip different nets in the right place, with one and the same tool.
How did you solve the customer's problem?
- We ended up constructing a motorized lifting yoke with long legs that sticks into the holes on the reinforcing mats. The legs were provided with feet, and a challenge was to get the feet big enough to hold the load, but at the same time small enough to fit in the holes in the most fine-meshed nets, without compromising on safety. First, we made prototypes that we tested at a local producer. We had to think outside the box and make adjustments along the way, scrapping several ideas before we found a good solution that filled the customer's needs.
You built intelligence into the tool, what does that mean?
- For example, we designed a tilt sensor that warns when the slope is too great. At over 10 degrees of tilt, an integrated light signal shines, while preventing the traverse from continuing to lift. You then must lower the load and take a new approach. Another feature is that the control of the lifting tool is integrated into the controls of the traverse control system.
Could you offer the customer anything more than our competitors?
- Yes, absolutely. Lifting reinforcing mats in this way is completely new. We have extensive experience of customized lifting solutions that we can benefit from when it comes to finding this type of new solution.
Any fun memories from the project you'd like to share?
- The customer was very generous ... When they sent a whole truck of reinforcing mats from Greece, we were a little shocked. We thought they were going to send two, three bundles that we could test lift. The whole thing would also be sent back. It was a big challenge just to unload and load the truck. We had built a lifting tool for the purpose but didn't have the peripherals needed to use it. There were many of us involved and had to improvise, but in the end we succeeded.
Was the customer satisfied with the final product?
– Yes, they have been using the tool continuously every day, eight hours a day, for three years without any reported problems. They are very happy, so happy that they turned to us again. This summer we sent them yet another tool.
Name some of Special Products’ main strengths
- In addition to rigorous requirements for safety, we have short lead times and work closely with the customer. There is a direct contact between the designer and the end customer to ensure that they get what they want. In addition, the price should be competitive, and it definitely was on this project.